Some updated pics.
Pressure pot back from powder-coating, with fresh piping and gauge
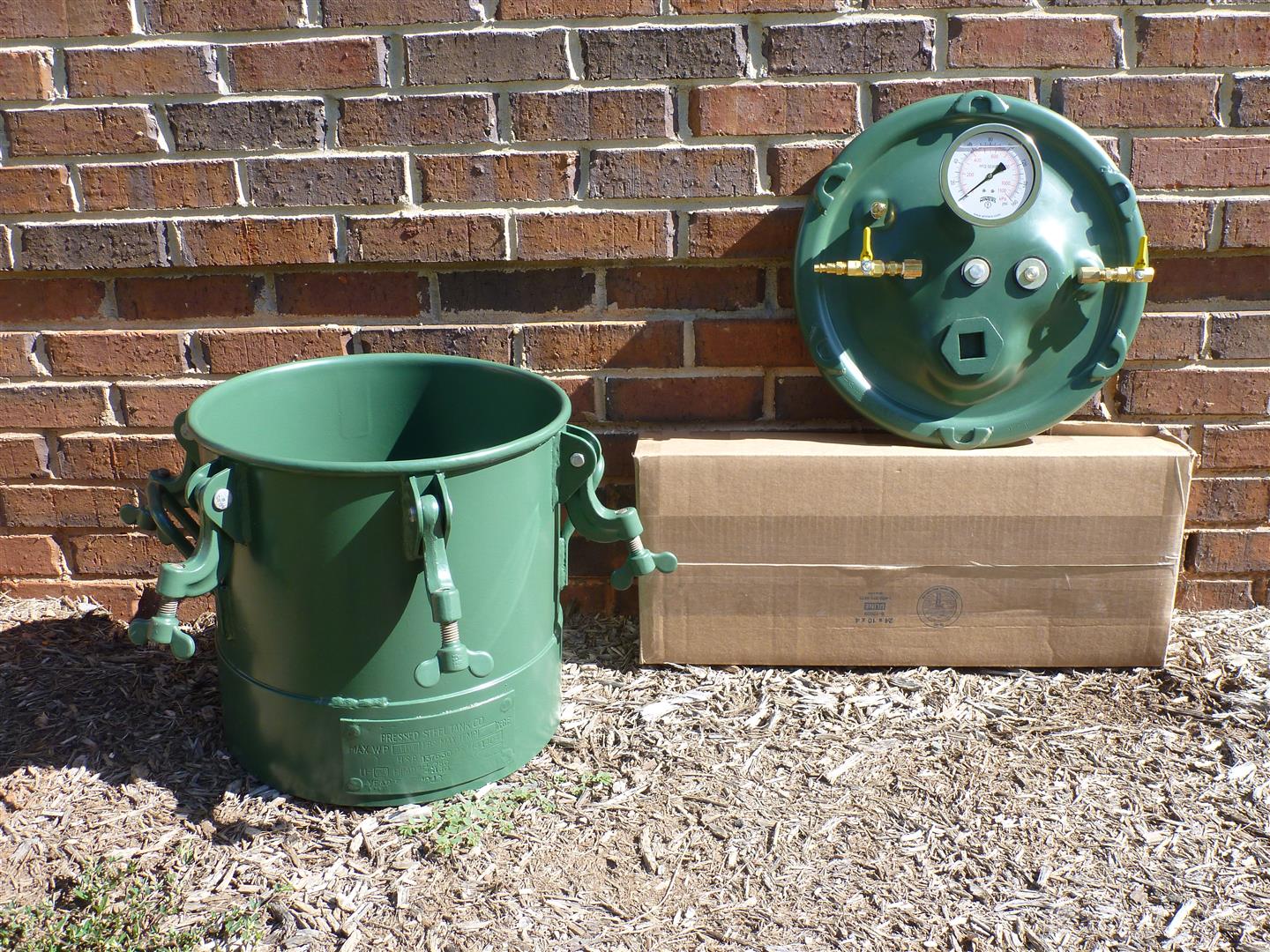
Used a large dial gauge mostly for style, but also to help see it better indoors
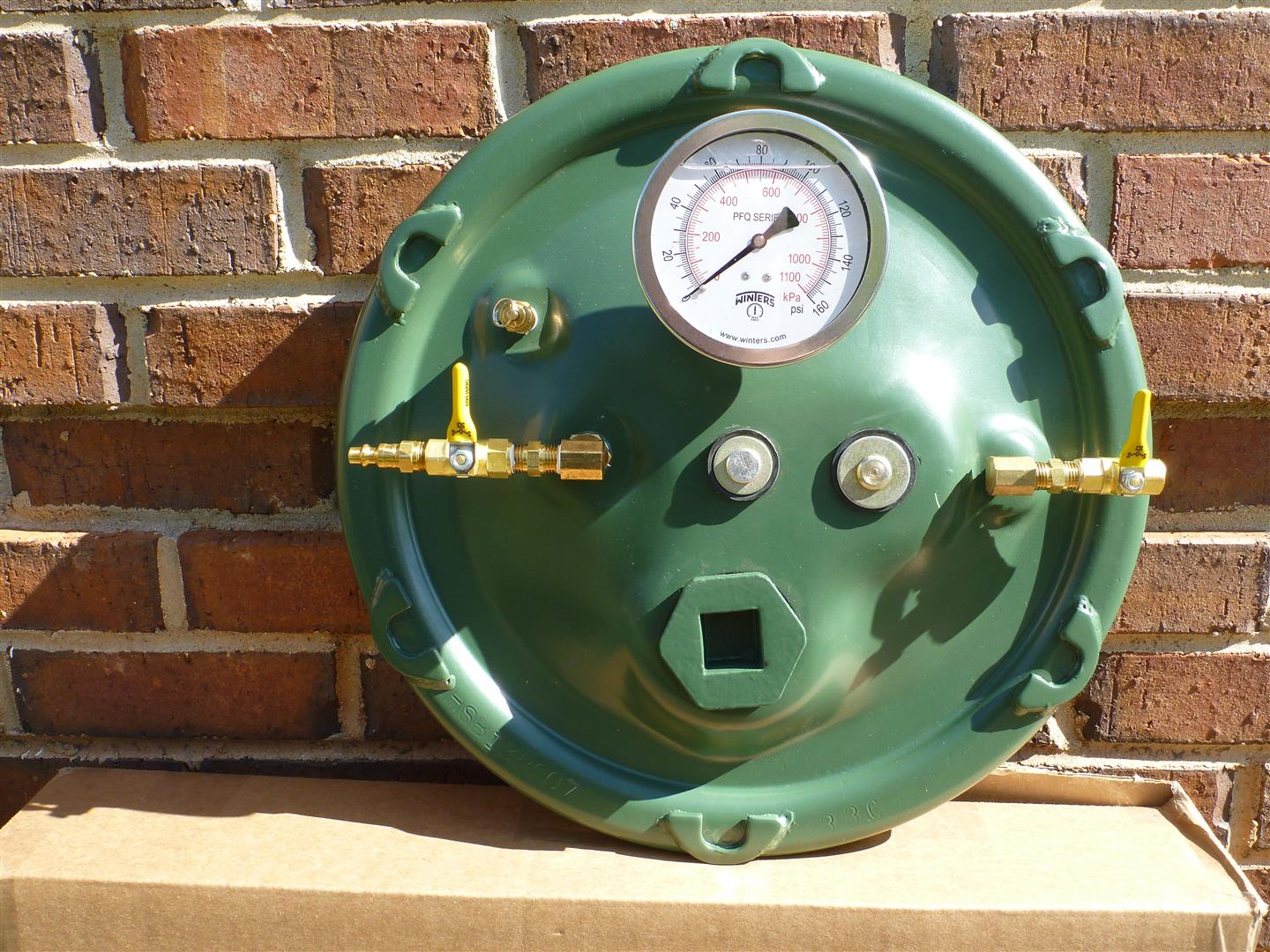
Interior of lid, showing the fittings used to close the two large openings.
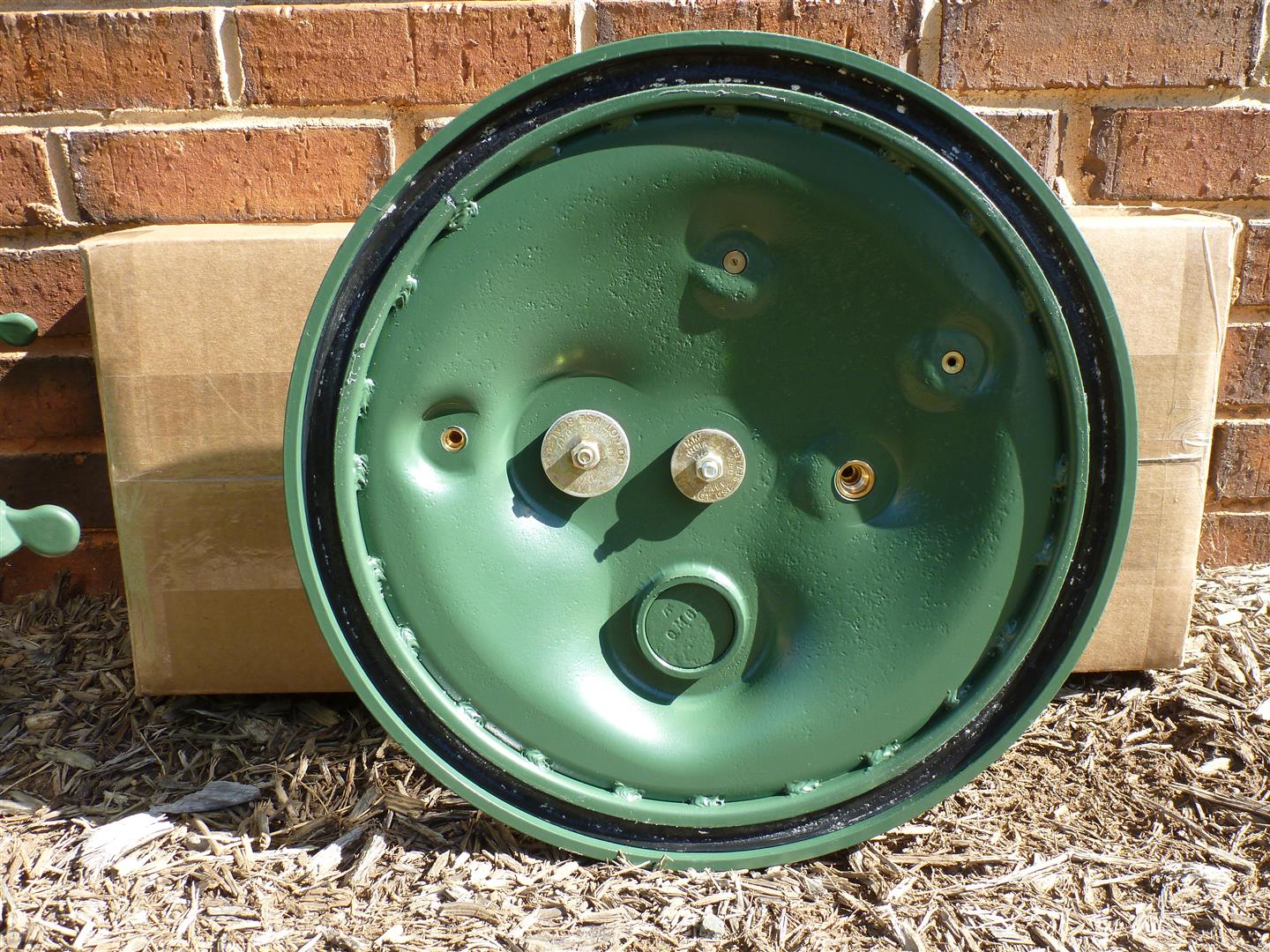
Pipe plugs, installed backwards so the plate side is inside the lid - better security against blowouts. Some pitting in the metal, but none of it serious. Seal was in good shape, apart from embedded paint residue, but I used almost a whole tube of aquarium sealer to run a bead along both sides of the seal for maximal air sealing.
Big old pressure pot
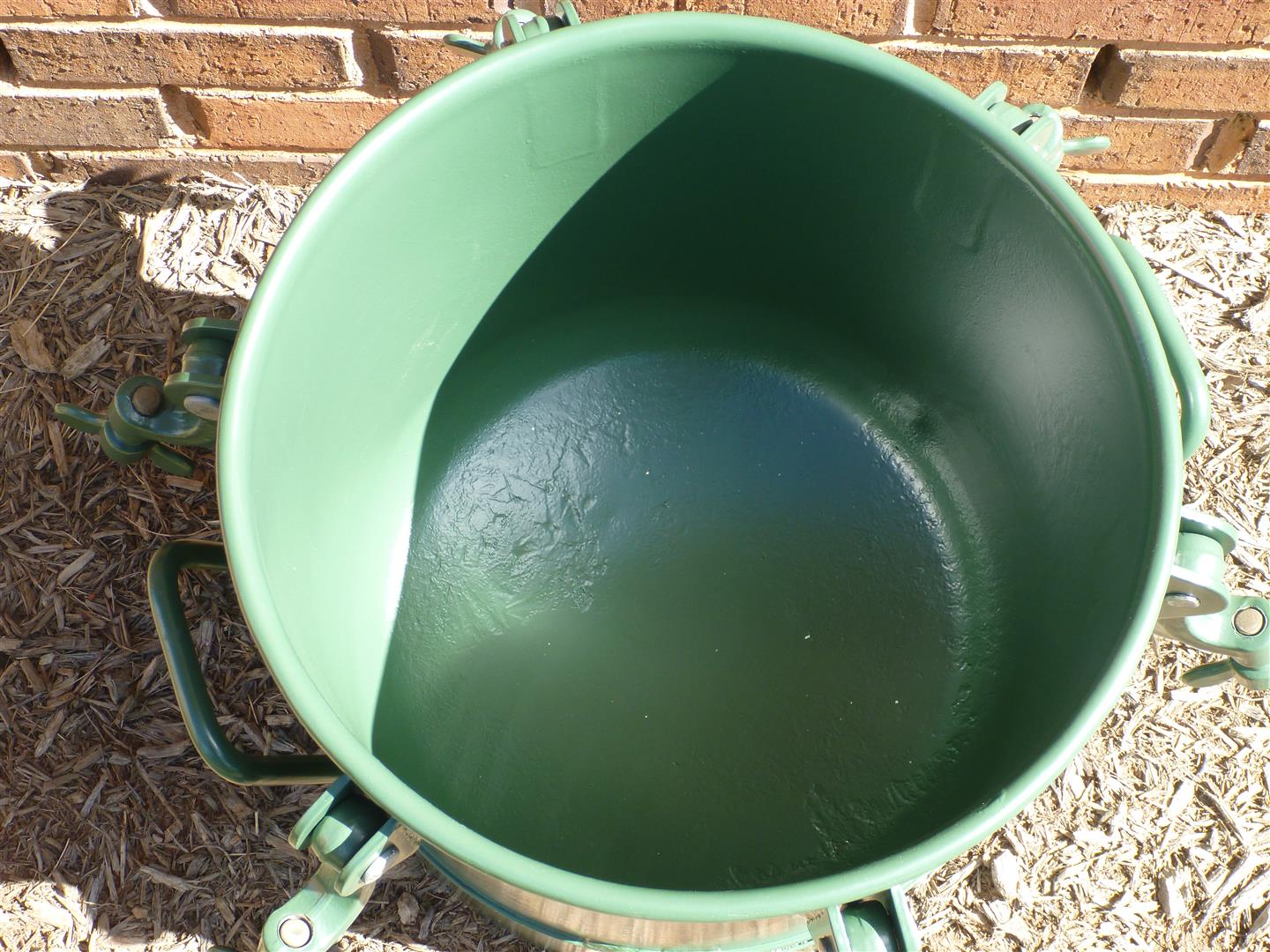
Galvanized finish was flaking off in some areas, the paint shop media blasted it before powder-coating
Air compressor. Loud.
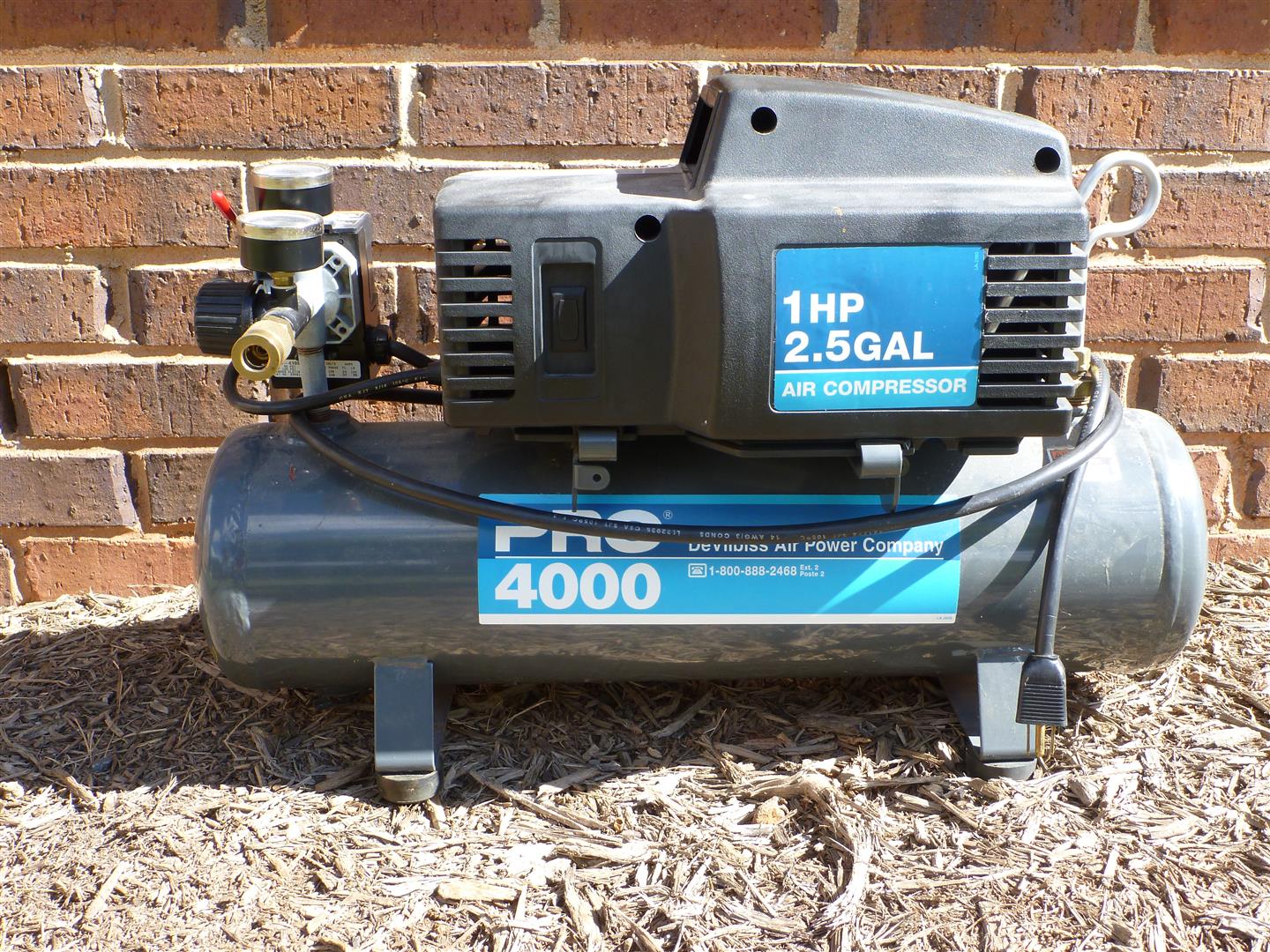
In the garage, going to try a pressure test later today, once the neighbors are all awake.

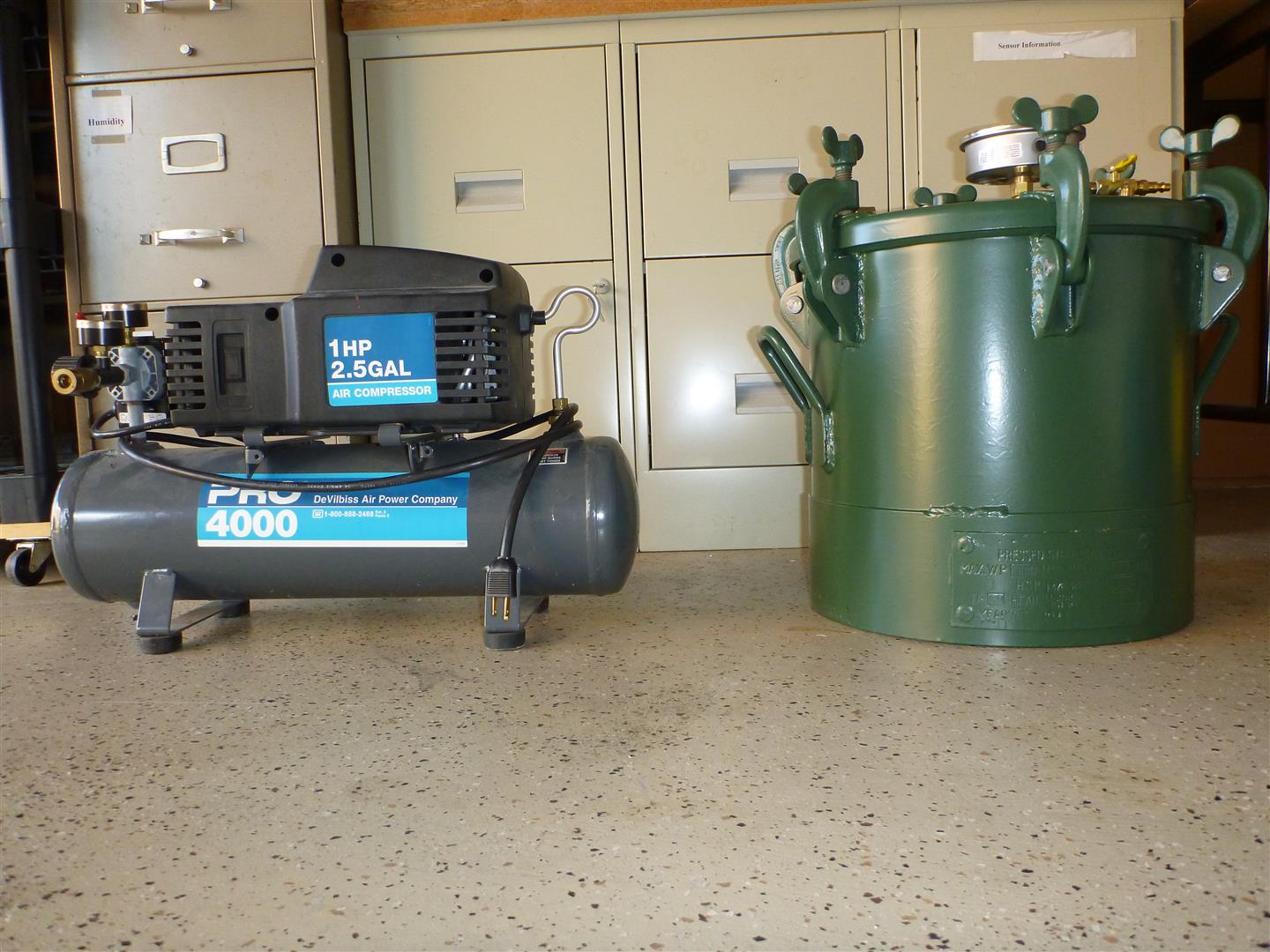